ENERGY EFFICIENT MOTORS IN PUMPING SYSTEMS
Typical high efficiency motor curves (150 kW, 4-Pole)
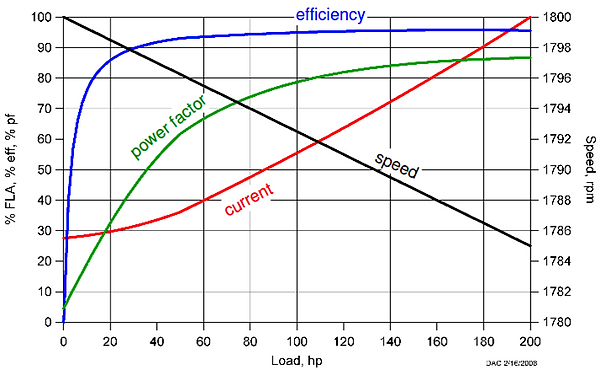
New High Efficiency motors have a very flat efficiency curve all the way down to 25-30% of full load. Pumps usually have power requirements in the area where the motor efficiency curve is flat. Therefore the motor is generally not a cause for concern in pumping systems, unless it is very much oversized.
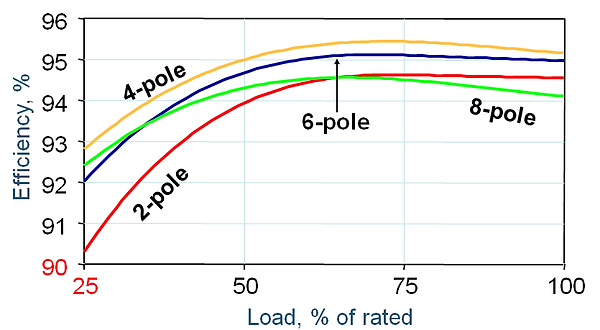
It is worth noting that there may be a few percentage points of efficiency that can be gained if the motor in service is very old or degraded. It will almost never be cost effective to simply replace a standard efficiency motor with a premium efficiency motor, however (as long as the existing motor is functional).
Motor improvements
- Determine existing condition of motors
- Electrical measurements
- Motor circuit analysis, infrared thermography
- Efficiency
- Plan ahead for repair/replace options
- Use MotorMaster software to evaluate savings by upgrading to a premium efficiency motor
- Application of variable speed drive will impact new motor type
- Evaluate how pump upgrades may effect the motor
- Opportunity to resize the motor
- Effect of variable speed drive
- Impact on motor service factor
- Determine how motor upgrades will impact pump performance
Whether the replacing of an energy efficient motor can reduce energy consumption in a pumping system?
This question can sound strange but sometimes it can happen.
High-efficiency motors have less slip and more speed of rotation. In accordance with affinity laws
- The Higher rpm of premium efficiency motors will increase pump capacity and power.
- The absorbed power is roughly proportional to the cube of the speed!!! A 2% speed increase could lead to 8% higher power usage
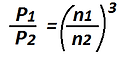